The 3D Home Printing Market is an emerging sector within real estate and construction, with the potential to revolutionize the way homes are built in the future. While still in its infancy, 3D printing in construction is making significant progress in both technology and application, gaining traction due to its ability to provide affordable, sustainable, and customizable housing solutions.
So What is 3D House Printing?
3D house printing, also known as additive manufacturing in construction, is a process that uses large-scale 3D printers to build homes by layering materials like concrete, polymers, or other composites. These printers are guided by digital models to create the walls, floors, and even some structural elements of a home. The technology can significantly speed up the construction process while reducing labor and material costs, making it an innovative solution for affordable, sustainable, and custom-designed housing. Check out this 60 Minutes episode for an eye opening introduction for the future of home construction – including construction on the moon!
What is the Market Outlook for 3D Home Printing?
- Market Growth: The global 3D construction printing market is growing rapidly. As of 2023, it is valued at about $1 billion and is projected to grow significantly, with an expected compound annual growth rate (CAGR) of around 91% from 2023 to 2030.
- Adoption: While 3D printing of homes is still in the early stages, there have been a few notable projects around the world. Companies like ICON and Mighty Buildings in the U.S., WASP in Italy, and Apis Cor in Russia are leading the way. These companies have already printed functional homes and are receiving attention for their potential to address housing shortages and provide affordable solutions.
- Government and Corporate Support: Several governments, especially in developing nations, are exploring 3D printing to address housing shortages. For example, in the U.S., non-profits like New Story are building 3D-printed communities for underserved populations. NASA is working with ICON to build landing pads on the moon and the US Military is also working with ICON to build military structures.
- Governments: In the Middle East, Europe, and Latin America are also starting to explore this technology.
Future Trends in the 3D Home Printing Market
- Increased Affordability: One of the biggest advantages of 3D home printing is its potential to drastically reduce construction costs. Labor costs are lower since the process is more automated, and the materials used in 3D printing—typically a mix of concrete and other composites—are often more cost-effective. As the technology scales, prices will continue to drop, making 3D-printed homes accessible to a wider range of buyers.
- Sustainability: With growing concern over climate change and environmental impact, 3D printing offers a more sustainable construction method. The process produces less waste, uses fewer materials, and can utilize recycled materials or locally sourced raw materials. Expect increased interest in eco-friendly 3D-printed homes, especially in markets focused on green building.
- Customizable Designs: 3D printing allows for far greater design flexibility than traditional construction methods. Builders can create custom shapes, curves, and designs without the added cost typically associated with such architectural features. This will drive future demand as homebuyers look for personalized living spaces at lower costs.
- Speed of Construction: 3D printing can drastically reduce construction time—some homes can be printed in 24 to 48 hours, excluding additional time for electrical, plumbing, and finishing. As the technology advances, we can expect further reductions in construction timelines, making it ideal for areas that need quick housing solutions, such as disaster relief zones.
Benefits of 3D Home Printing
- Cost Efficiency: 3D-printed homes are estimated to be 20-40% cheaper than traditionally built homes. This cost advantage stems from reduced labor, faster construction times, and the use of affordable materials.
- Speed: Homes can be printed in days rather than months, which reduces labor costs and accelerates the time to occupancy.
- Sustainability: The method uses less material waste, reduces carbon footprints, and allows for the use of sustainable or recycled materials.
- Customization: Homeowners can opt for unique and intricate designs that are harder to achieve with traditional methods, offering personalized living spaces at a lower price point.
- Addressing Housing Shortages: In regions with housing crises or areas affected by natural disasters, 3D home printing can provide rapid, cost-effective solutions for temporary or permanent housing.
Drawbacks of 3D Home Printing
- Limited Material Options: Currently, the range of materials that can be used for 3D printing homes is limited. Most construction is done with concrete or cement-based materials, which may not meet all architectural or geographical needs. Innovations in material science are still needed to expand options.
- Regulatory Hurdles: Building codes and regulations vary widely across regions and can be a significant barrier. Many municipalities and governments have not yet developed guidelines for 3D-printed structures, slowing down broader adoption.
- Infrastructure Challenges: While 3D printing can handle the core structure of homes, traditional methods are still needed for plumbing, electrical systems, and finishing touches, which increases overall construction time.
- Skilled Labor: Though automation reduces the need for large construction teams, there is still a need for skilled workers to operate 3D printers, oversee the process, and complete post-printing work. As the technology grows, there will be a learning curve in developing a workforce proficient in 3D home printing.
- Scalability: Much like the adoption of highly transformative infrastructures, like Electric Vehicles, there is a challenge currently with scalability to drive efficiency and speed in volume with 3D home printing.
- Public Perception: 3D-printed homes are still a novel concept, and some buyers may be skeptical about the durability, safety, and aesthetic appeal of these homes compared to traditionally built ones.
Maintenance Considerations
While 3D-printed homes offer numerous benefits like affordability, sustainability, and speed of construction, it’s essential to be aware of potential maintenance needs—especially for systems that go beyond the printed structure itself.
- Electrical Systems: Since 3D printers currently focus on building the walls and core structure, traditional methods are still needed for installing wiring and electrical systems. Ensuring that your home has a solid plan for safe, efficient electrical integration is crucial, just like in any other home.
- Plumbing: Plumbing is another key system that will need conventional installation methods in 3D-printed homes. Planning for proper piping, drainage, and potential future repairs should be a priority. Consider discussing with your builder how these systems are incorporated to ensure they meet local building codes and long-term functionality.
- HVAC: Heating, ventilation, and air conditioning systems (HVAC) in 3D-printed homes are installed similarly to traditional homes. Since 3D printing allows for customized design, it’s important to work with a professional to ensure the HVAC system is well-suited for your home’s unique layout, insulation, and airflow needs.
Overall, while the 3D printing process streamlines construction, key infrastructure like electrical, plumbing, and HVAC systems still require thoughtful planning and expert installation to ensure a fully functional, maintainable home.
Correcting an infrastructure issue in a 3D-printed home is similar to addressing the issue in a traditionally built home, but there are a few unique considerations due to the nature of 3D-printed walls and structures.
ACCESS: In 3D-printed homes, infrastructure is usually installed inside channels that are either pre-planned during the design phase or carved into the printed walls after construction. To correct a problem:
- Locate the issue: Infrastructure systems should have accessible shut-off valves/panels and issue detection may require cutting into the walls to find the affected area.
- Cutting into the walls: While concrete or composite materials are used for printing, specialized tools (like a concrete saw or drill) may be needed to cut into the walls to reach the issue.
REPAIR: Once the issue is exposed, the process of repairing or replacing them is similar to traditional homes:
- Patch or replace: Depending on the severity of the issue, a patch may be applied, or the damaged section may need replacement.
- Re-installation: After the fix, any fittings or insulation will need to be restored to ensure the issue remains secure and efficient.
WALL REPAIR: Once the repair is completed, the wall itself will need to be patched:
- Fill the opening: The opening in the 3D-printed structure is typically filled with a compatible material, such as concrete or plaster, to restore the wall’s integrity.
- Repainting or refinishing: After the patching material dries, it will need to be sanded and repainted to match the rest of the structure.
Challenges and Solutions
- Wall material: Since 3D-printed walls are often made of concrete or other durable materials, accessing infrastructure can be more labor-intensive compared to drywall. Using scanning technology or referring to the original 3D design plans can help reduce the amount of cutting required.
- Design for maintenance: Builders of 3D-printed homes may incorporate design features that allow for easier access to systems, such as built-in service panels or modular components.
Overall, while the materials used in 3D-printed homes add some complexity to accessing systems, the repair process is quite similar to traditional construction once the infrastructure is exposed.
Where is the Market Headed?
- Mass Adoption in Developing Markets: Countries with significant housing shortages or high demand for affordable housing will likely be early adopters. 3D printing could help resolve these issues quickly and at scale. Regions like Latin America, Africa, and parts of Asia could become hot spots for 3D-printed homes in the next decade.
- Innovations in Materials: Expect advancements in the types of materials used for 3D home printing. New composites, eco-friendly materials, and even materials sourced from local environments (like sand or dirt) will expand the possibilities for what types of homes can be printed and where they can be built.
- Mainstream Adoption in 5–10 Years: While still in the early stages, 3D home printing could become mainstream by 2030. As the technology matures and regulatory hurdles are addressed, we’ll see more developers and builders adopting it for both affordable housing and custom-built homes. By 2030, it is anticipated that 3D-printed homes could constitute a noticeable portion of the global housing market.
- Commercial and Industrial Applications: Beyond residential homes, we will likely see 3D printing adopted for commercial and industrial construction. Warehouses, office spaces, and even retail buildings could be printed with similar benefits of speed, cost efficiency, and customization. Walmart has already given it a test drive with one of their newer warehouses as the largest commercial endeavor to date.
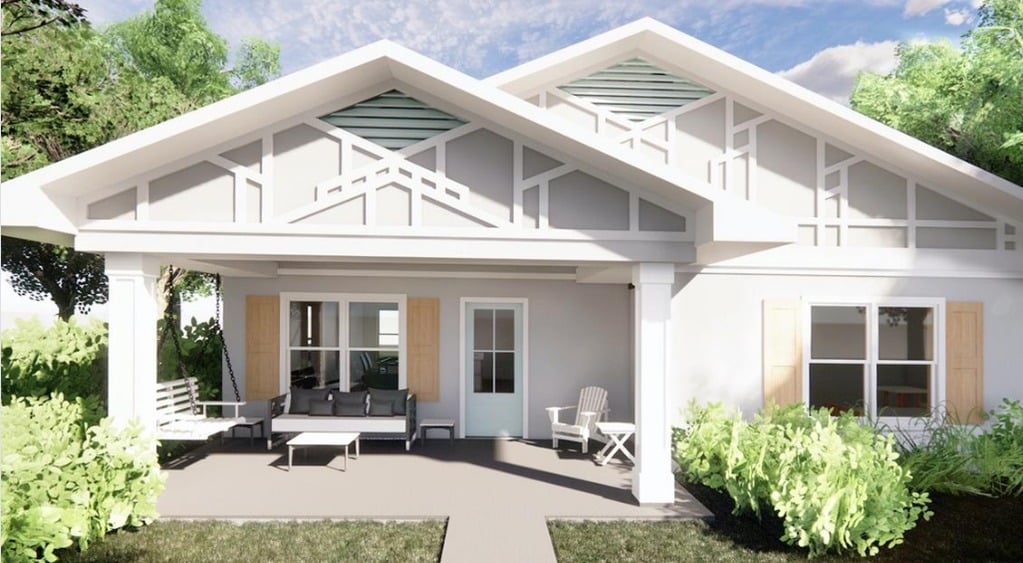
Richmond’s first 3D Printed Home – Virginia Housing
Virginia’s first 3D Printed Home in Richmond, VA.
3D Home Printing Activity in Virginia: A Growing Innovation
In Virginia, the use of 3D home printing is still in its early stages, but the state is showing promising signs of adopting this innovative construction method. Key highlights of 3D home printing activity in Virginia include:
- Affordable Housing Initiatives: Like many states, Virginia faces a housing affordability challenge, particularly in urban and high-demand areas. 3D printing is gaining attention as a potential solution for providing affordable housing quickly and cost-effectively. Local governments and non-profits are beginning to explore the feasibility of 3D-printed homes to meet the demand for affordable housing. First 3D printed home in Richmond with Habitat for Humanity and another in Williamsburg – noting VA Tech involvement.
- Research and Development: Several universities and construction tech companies are starting to look into 3D printing technology as part of broader efforts to innovate the building process. Research into sustainable materials and cost reduction is actively underway, aligning with the state’s interest in more sustainable, eco-friendly building practices.
- Pilot Projects: While large-scale 3D-printed communities have yet to take root in Virginia, there have been small pilot projects and demonstrations showing the potential of 3D printing in construction. These projects often focus on single-family homes and aim to highlight how the technology could reduce construction costs and build times soon. Pulaski Virginia project – has been cancelled due to costs.
- Regulatory Landscape: One of the biggest challenges to 3D home printing in Virginia (and across the U.S.) is navigating the building codes and regulations. Virginia is gradually updating its regulatory framework to accommodate new construction technologies like 3D printing, but widespread adoption will require more alignment with local zoning and safety standards.
Bottom Line
When Will 3D Home Printing Materialize?
While the technology is advancing rapidly, widespread adoption will likely take another 5–10 years. Early adopters are already seeing the benefits, but full-scale implementation in mainstream residential construction depends on overcoming regulatory, material, and market challenges. By 2030, we can expect 3D printing to be a regular option for homebuyers, particularly in markets focused on affordable housing, sustainability, and innovation. The same holds true for Virginia.
The truly heartwarming component of this technology and its application is starting with the underserved and the “missing middle” with affordable solutions to the challenges of homelessness and lack of affordable housing. Layer in eco-friendly and sustainable homes that survive fire, hurricanes, floods and we have a winning combination of technology meeting construction!
As always . . .
Be sure to check out the:
- Home Valuation Tool
- Reach out for your personalized Home Value Report
- Calculate your future mortgage
Don’t forget the Home Buying and Selling Guides !
Never miss an issue by subscribing below and I look forward to speaking with you soon about your free Home Preparation and Market Analysis consultation!